Ra roughness, in mechanics, is an average value characterizing the surface condition of a part or material.
In industry, roughness control is part of the dimensional validation process and ensures part conformity during machining.
While there are other indicators that characterize surface roughness, this article will focus on the general surface condition of the control area.
Table of Contents
What is the roughness Ra?
Definition
The Arithmetic Average Roughness, denoted as Ra, is the absolute average deviation relative to the base length.
Simply put, the Ra value indicates the average surface roughness for the length of the measurement performed, i.e., the mean difference between peaks and valleys.
To visualize roughness, we can imagine a two-dimensional cross-section of the surface. The higher the Ra roughness of this surface, the greater the difference between the peaks and valleys.
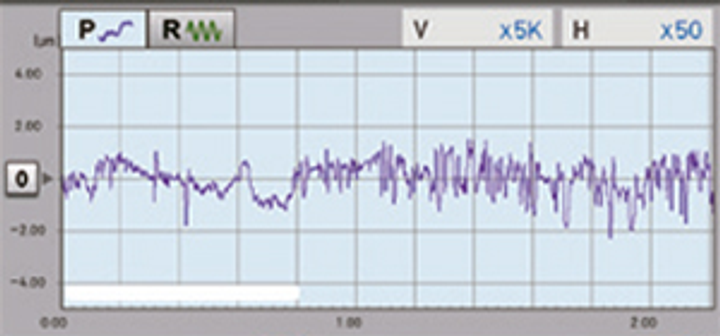
Ra roughness is an excellent method to quickly verify that the surface meets the customer’s specifications, as its value is representative of the overall surface condition.
Why should you care about the surface roughness?
In certain sectors, particularly high-technology industries, it’s crucial that the Ra roughness of manufactured components meets precise expectations.
Roughness plays an important role in mechanics, it allows to control phenomena such as fluid flow or adhesion. It’s a critical dimension in precision mechanics due to its significant impact on friction force, wear, and mechanical anchoring (among other factors).
When the average roughness of a surface is determined using the Ra indicator, it is possible to quickly determine the micro-or macro-geometric irregularities of the surface.
This is how parts can be classified as compliant or non-compliant during the quality control process.
Other roughness indicators
In addition to Ra, when evaluating surface condition, other indicators like Rz or Rt can provide additional valuable information:
- Rt defines the total roughness recorded, i.e. the sum of the maximum peak with the maximum valley. This is the largest distance recorded for the measurement.
- Rz defines the regularity in the recorded measurements. It is an average of the five largest total deviations (Rt) recorded for length.
These indicators allow for a more precise understanding of the surface’s macro-geometry.
They’re often used as selection criteria in quality control, and modern measuring instruments typically include them in their results.
Measuring RA roughness of a surface
Various tools are available to measure the Ra roughness of a surface. Choosing a tool depends primarily on the control requirements and specific needs of the measurement.
Roughness meters (Profilometers)
A roughness meter, or profilometer, is a contact measuring device that quickly determines the Ra roughness of a surface.
The main advantage of these devices is their simplicity and portability. To perform a measurement, you simply place the device on the surface to be inspected and activate it.
There are two types of roughometers: skid and non-skid profilometers.
In the first case, the device has a small skid at the end of its measuring head that slides on the control surface, serving as a straight guide.
The skid can affect the measurement if the surface isn’t flat, so it’s best used on the flattest possible surfaces. Despite this limitation, skid profilometers are very handy and efficient tools for measuring flat surfaces.
Skidless devices use an internal guide that calculates the probe’s orientation in 3D space, enabling measurements on non-planar surfaces.
The ability of skidless devices to recalculate trajectories allows for more accurate control, whereas skid devices might complicate or distort measurements when the surface has slight variations.
Optical Measurement
While Ra roughness can be easily calculated with roughness meters, these are mechanical devices requiring physical contact between the probe and the surface.
For higher accuracy, it’s preferable to use an optical measuring system such as an interferometer.
Interferometers are sophisticated measuring devices capable of mapping the surface topography of any material.
They’re significantly more accurate and efficient than contact measuring systems because they utilize interference effects produced when light is projected onto and reflected by the measurement area.
This is currently the most efficient method for obtaining highly accurate surface roughness values.
Indirect control of surface roughness
Sometimes, direct measurement of surface condition is impossible due to inaccessibility of measuring devices. This can occur for several reasons, primarily:
- The need to disassemble an assembled part to bring it to the measurement laboratory.
- The part is too bulky and it is difficult to position it for the measuring machine.
- The area to be checked is unreachable by your control instrument.
In this kind of situations, the ability to indirectly measure the part would be extremely handy. This is precisely why Plastiform has developed impression products capable of performing such operations.
Indirect, delocalized Ra Roughness Control
Plastiform has developed impression products. These products allow the properties of the control area, including its surface finish, to be copied with great precision.
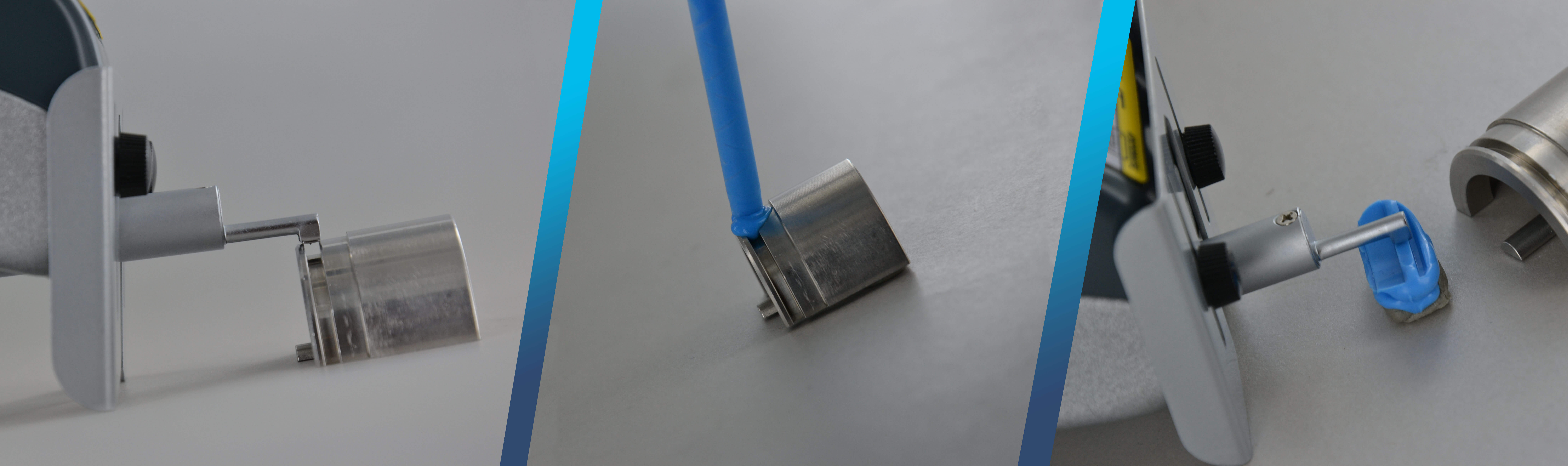
If, for any reason, you cannot directly measure the part, Plastiform will undoubtedly help to solve this problem.
P80 Ra is a pasty impression product (which adheres to the surface, even if it is overhanging).
By applying it to your part, you can replicate its properties. The product then stiffens to 80 Shore A, allowing you to easily perform measurements on the impression using your usual measuring devices.
Check Ra Roughness on a Plastiform impression
The accuracy of the measurement will vary depending on the measuring instrument you use.
We recommend non-contact measurement devices, such as white or green light interferometers, which are highly accurate and suitable for measuring the surface condition of impressions.
If an interferometer isn’t available, opt for a skidless profilometer, which is more suitable for measuring the roughness of an impression. Both profilometers and interferometers will provide accurate Ra values, but interferometers offer higher precision for other roughness indicators.
Skid roughness testers also work well on our impressions. However, they provide rough estimates of Ra, and other values (Rt and Rz) may be distorted due to the pressure exerted by the skid on the impression.
At Plastiform, we recommend performing the impression checks with the devices for which we have validated the compatibility, i. e. Accretech and Sylvac.
Conclusion
Ra roughness is a key indicator of the surface macro-geometry of a part or material, reflecting the treatments applied during the production process.
To measure this indicator, we use various measurement instruments that measure the difference between “valleys” and “peaks” recorded over a given length and allow us to calculate several characteristics:
- Total roughness (Rt), Indicates the maximum deviation recorded over the measured length. Rt is calculated by adding the maximum peak to the maximum trough.
- Tegularity, (Rz), which represents the average of the five main Rt values over the measured length.
- Arithmetic Mean Roughness (Ra), Indicates the average roughness of the controlled surface.
Ra is a particularly important parameter as it directly characterizes the overall surface condition, enabling a comprehensive evaluation.
To check the surface condition, various devices can be used, both contact and non-contact. Typically, profilometers or interferometers are employed for Ra roughness measurement.
Sometimes it’s impossible for these devices to access the desired control area. In such cases, Plastiform offers a valuable solution.
Use Plastiform to replicate the control area and perform your Ra roughness measurements directly on the impression with your measuring devices!
Choose our Personalized Kit to get everything you need to try impression-based Ra roughness controls!