During machining, no matter how precise the machine used is, surfaces will always have irregularities. These irregularities are micro-geometric roughness caused by the imperfection of cutting tools (yes, perfection doesn’t exist!).
Measuring these imperfections is crucial. For over 80 years, surface finish measurement has been used to improve product performance. By qualifying the average of these defects, it is possible to determine whether a surface meets specifications.
The roughness tester is one of the instruments capable of qualifying the surface condition of a part.
Today, surface finish has multiple parameters (according to international standards): The P parameters, calculated on the primary profile, the R parameters measured with the roughness profile, and the W parameters corresponding to the waviness profile measurement.
In this article, we will take a look at the different roughness testers capable of measuring some of these parameters and provide insights into techniques and instruments for further exploration.
Table of Contents
Surface Condition Parameters
To describe the condition of a surface, it is generally necessary to measure several profiles, two of which are of interest in this article: the roughness profile and the waviness profile. Each provides information about surface defects.
Roughness
Roughness concerns micro-geometric defects and is measured with a roughness tester or profilometer. Parameters related to roughness have the prefix R: Ra, Rz, Rw, etc.
Roughness measures defects such as striations or grooves caused by machining tools.
Waviness
Waviness is complementary to roughness and includes all surface finish components with a large wavelength. Waviness parameters begin with the letter W.
Roughness Testers on the Market
A roughness tester is a contact measurement instrument. Its stylus travels across the surface to extract various measurements related to roughness and waviness parameters in some cases.
Roughness testers are lightweight, low-investment instruments, making them one of the most accessible devices for inspecting product surfaces. However, there are different types of roughness testers.
Roughness Tester with Skid
This is the entry-level model. The stylus of this device is guided by a skid, allowing it to measure only flat surfaces.
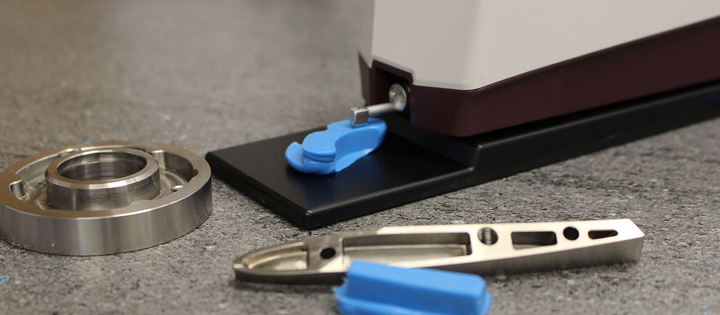
With a skid, the stylus can only measure roughness parameters. The skid guides the stylus but may affect measurement accuracy on certain surface types. However, the skid makes the device robust and easy to transport.
A skid-type roughness tester is suitable for workshop use, where quick and easy positioning of the device is required.
Roughness Tester without Skid
On the other hand, skidless roughness testers use an internal guide in the device to control the stylus. This internal guide can handle more complex surfaces.
Skidless roughness testers are often preferable as the internal guide allows the stylus to achieve better results.
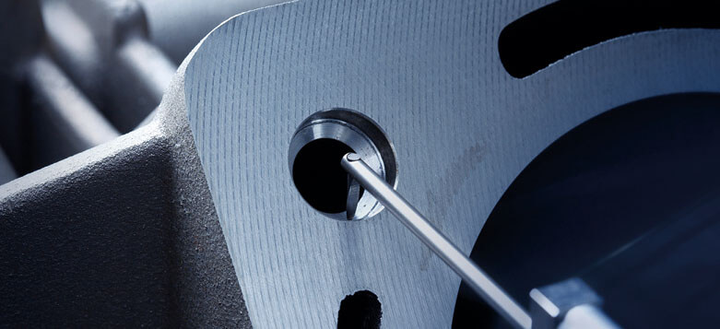
This is also an excellent choice for measuring Plastiform impressions.
Alternatives to Roughness Testers
Roughness testers are contact measurement devices. If you wish to measure roughness with a non-contact instrument or if it is impossible to position the roughness tester, there are alternatives available.
Profilometers
Profilometers were originally contact measurement instruments that read the surface to be measured using a diamond-tipped stylus. Do not be mistaken; contact profilometers still exist and are very practical and affordable. However, they have drawbacks:
- They are slow, with a stylus scanning speed of about 1 mm/second.
- They can scratch the surface, so they can only be used on hard surfaces (metallic).
- It is impossible to measure very fragile or abrasive surfaces without damaging the stylus or the surface.
Portable profilometers are what we call roughness testers, so their operation is relatively similar.
There are also optical profilometers, which are what interest us as alternatives to contact roughness measurement. Two types of optical profilometers are distinguished: matrix optical profilometers and scanning optical profilometers.
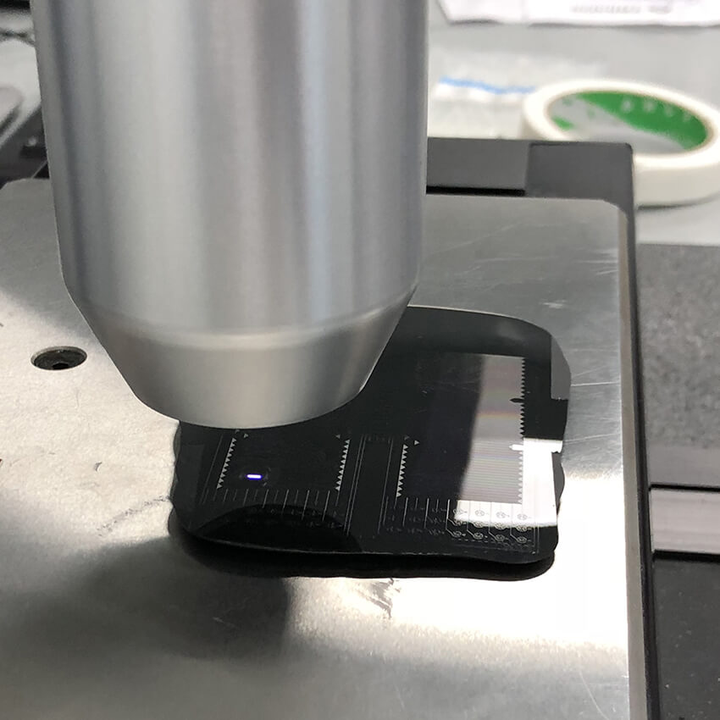
The first, the matrix optical profilometer, works by reading images taken with a CCD camera. The advantage of this model is undoubtedly its speed. It is the fastest on the market and offers very precise measurements.
In the case of the scanning optical profilometer, it is a bit more complex, as the use of a mechanical scanning device causes slight noise that overlaps with the surface profile. Of course, this type of profilometer remains excellent, and you may also find noise with a roughness tester due to mechanical friction between the stylus and the surface.
Indirect control
In some cases, your roughness testers cannot reach the surface to be measured, just as you cannot move the surface to a profilometer. Faced with this impasse, there are very few measurement instruments that can help.
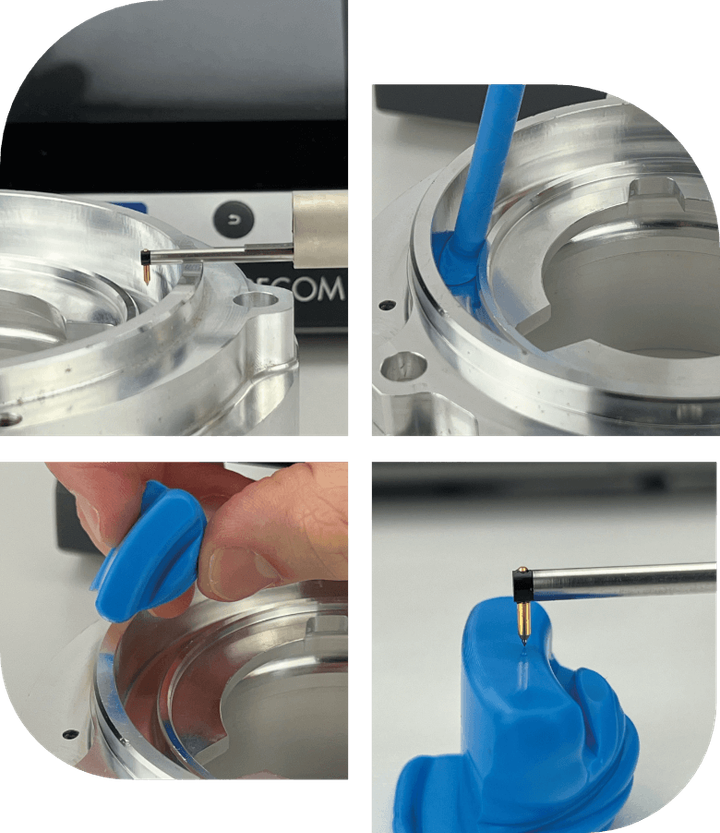
The best value-for-money solution is taking an impression: Using resin, replicate the surface and transport it to the roughness tester for measurement.
Plastiform offers industry-dedicated solutions with precise measurements down to the micron level for an average of $4 per test.
Our products are compatible with both roughness testers and optical profilometers. (And more broadly, all quality control instruments used for surface finish or dimensional control.)
The P80 Ra is a product specifically developed for use with roughness testers. If you encounter a problem with this type of device, I highly recommend taking a closer look at this product; it will solve your problem! It is even more precise when used with a skidless roughness tester!
The F30 Visual is more suitable for non-contact measurement devices; it is too flexible to be used on a roughness tester. While it’s not the focus of this article, it’s always interesting to know the range of solutions available: F30 Visual is for non-contact!
How to Use a Roughness Tester?
To answer quickly: It depends on the manufacturer! Each machine has its specificities, but the principle is quite similar:
- Always calibrate the roughness tester with its standard (it usually comes with the machine). Your measurements will be incorrect if your machine is not calibrated!
- Once your machine is ready to measure, place it on the surface to be examined and start the measurement. Normally, you should see the stylus moving. Let it work until it stops completely.
- Take a look at the device’s screen, it will display the data.
Some machines allow you to export the data for digital storage. Refer to your device’s manual for more information!
How to Measure with Plastiform?
Using a roughness tester with Plastiform is strictly the same as measuring the original surface; the only additional step is taking the impression!
We already have a lot of resources that will allow you to learn more about how to apply Plastiform products or extract an impression. If you are not familiar with our technologies, I invite you to consult them!
In the context of dimensional control, there is a small specificity that comes into play during impression taking.
Since we are going to perform the control with a roughness tester, we will need to position the impression. To do this, we will flatten the face of the impression opposite the surface to be controlled.
Simply flatten the paste with a flat surface when placing the applicator gun (before polymerization, otherwise, it will be impossible!). You have about 6 minutes with the P80 Ra to perform this operation!
When the product has polymerized, you can easily place it on the flattened face and perform the measurement with your roughness tester (with or without skid!).
Conclusion
The roughness tester is a surface finish measurement device that allows verifying the conformity of a part. With a skid-type roughness tester, you can retrieve the roughness profile of the surface. With a skidless roughness tester, you can also retrieve the waviness profile of the surface.
The roughness tester is an effective, reliable, and affordable instrument, and it works very well with Plastiform!
If you wish to systematically inspect your parts, a portable roughness tester with P80 Ra (in case of hard-to-reach areas) is a winning combination!