Threads are helical grooves commonly known as screw threads. When a thread is inside a cylinder (female thread), it’s called a tapped hole. Conversely, threading refers to an external thread (male thread).
Thread, bore, and tap inspection is a common requirement in industry, as numerous parts feature this type of geometry. Ensuring the conformity of their measurements is crucial. However, this operation is far from easy to perform, especially for custom threads.
Indeed, for inspection machines, it’s sometimes difficult to access certain corners of the part due to the geometry and dimensions of the pitch, or simply the entrance diameter of the hole in the case of a female thread.
When machining a part and you need to certify its measurements, gauges are not always the best option to ensure the dimensions of the machined part. This is where a profile projector can be particularly useful.
Table of Contents
Different types of threads
Standardized threads
There are several thread standards worldwide. They differ mainly in their geometry (flat crest, rounded crest, etc.) and pitch dimension (metric, imperial, etc.)
Here are the most common threads in the industry:
- Metric thread SI (International System) – Crests and roots are flat, the angle is 60°, and units (diameter and pitch) are in millimeters.
- US thread (UNC and UNF) – Crests and roots are flat, the angle is 60°. The diameter is in inches and the pitch in threads per inch.
- Whitworth thread – This is a British-origin thread. Crests and roots are rounded, the angle is 55°. The diameter is in inches and the pitch in threads per inch.
These three references are the most common in industry, and their inspection must be carried out rigorously to comply with current standards (ISO, for example).
When trying to inspect a standardized thread, you have many more options than for its tap.
Indeed, on the outside, space doesn’t constrain you from using measurement tools as you wish, and the part can even be positioned on a profile projector for precise inspection.
By using a gauge, you can easily verify the conformity (or non-conformity) of a part (with relative visual inspection, however). However, a profile projector offers more accurate and objective measurements.
Specific threads
Some sectors use their own threads to meet requirements specific to the industry or the reference assembly.
Although these threads have been standardized, it’s often more complicated to perform quality control easily. There are many standards, but the issues encountered in this case are often identical.
Sometimes, the necessary precision is very important to control not only the conformity of the thread but also its wear. In the second case, control can quickly become tedious and costly to perform, as it requires disassembling the part and moving it. A profile projector can be invaluable in these situations, offering precise measurements without the need for disassembly.
Thread Inspection: What Are the Solutions?
Thread gauges
For standardized threads (and more broadly, standardized threads), inspection gauges exist, called thread gauges.
The instrument resembles a Swiss army knife that combines several thread testers. The tester is supposed to fit perfectly into the thread if it’s correct.
The operator can visually verify that the thread corresponds to the standard according to which it was created. However, this method lacks the precision offered by a profile projector.
Threaded Gauge
The threaded gauge works in a similar way to the thread gauge. It’s a standardized thread onto which you should be able to screw your thread.
The operation is simple: if you can’t screw the thread properly, it’s not compliant. While effective, this method doesn’t provide the detailed measurements that a profile projector can offer
Digital Imaging Control
When you’re looking for precise data, gauges don’t meet your needs. Moreover, they don’t allow for traceability in your control process.
Digital imaging is now a widely used technique for controlling various shapes, including threads (external threads). A profile projector is a prime example of this technology.
Using these control devices, it’s very easy to make very precise measurements on external threads. However, it’s very difficult to perform internal controls on tapped holes, for example (and more generally, on internal dimensions that are difficult to access). This is where a profile projector truly shines, as it can provide accurate measurements of both external and internal threads.
Indirect Relocated Thread Control
Less known but very effective. This control technique aims to relocate the control by using an intermediary (an imprint) of the area to be controlled.
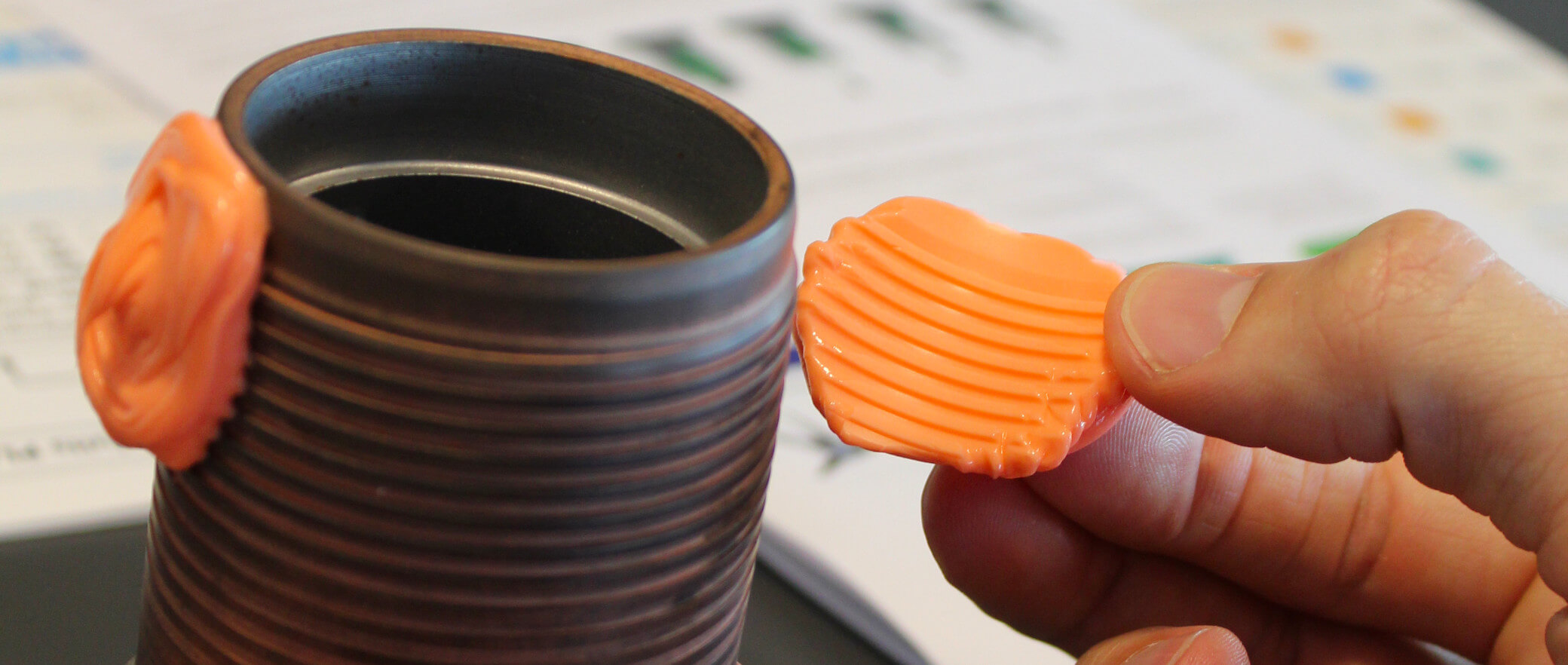
When you’re looking to perform a measurement control of an internal thread, being able to perform the control on an intermediate imprint can be very practical, among other things, for:
- Not wasting time disassembling, moving the part to the control machine, and reassembling it.
- Controlling an internal thread without having to destroy a part to make it measurable on a digital vision machine or profile projector.
- Performing systematic controls or more frequent wear controls thanks to the benefits of the first two points.
Indirect relocated control is a very economical, fast, and easy-to-implement technique. It’s very interesting for sectors where parts can be very expensive to produce.
Thread control by IMPRESSION TAKING
Impressions are excellent for making imprints of internal and external threads.
Indeed, even if it may seem easy to control a male thread, it is sometimes more cost-effective (in terms of time and finances) to control the thread with an imprint anyway.
This is, for example, the case in sectors such as oil, gas, and energy, which have threads on bulky or difficult-to-move parts.
How does it work?
At Plastiform, we use bi-component products that are originally liquid, pasty, or malleable.
When the two components are brought into contact, the product hardens while remaining very elastic. It’s thanks to this property that it’s very easy to extract the imprint of a female thread, for example.
With the imprint thus extracted, you can easily perform your measurements, but also and above all, keep traceability of your control by preserving the imprint. These imprints can then be measured using a profile projector for precise, repeatable results.
Which Plastiform for My Thread Inspections?
The choice of product is generally linked to several factors:
- The application you’re looking to perform: dimension control, surface condition control, roughness control, etc.
- The difficulty of extracting the replica – the more difficult it is, the more flexible and resistant to elongation the replica must be.
- The initial consistency: should the product be liquid and flow, pasty and maintain its shape, or malleable and directly manipulable by hand.
Thread inspection is an application very often performed by the Plastiform range. As a result, certain products have stood out as being very practical for performing certain types of inspection, especially when used in conjunction with a profile projector.
Thread with Nominal Diameter Less than 20mm
Only a very liquid and penetrating product will be suitable for a very fine diameter thread. The F20 combines all the properties necessary for such an impression and is very easy to extract if your part also has an extraction constraint.
Impression on a Female Thread (Internal)
For an internal thread with a nominal diameter greater than 20mm, two scenarios must be considered. First, if you’re looking for a total impression of the thread. In this case, you’ll need to take into account the difficulty of extraction. Generally, you’ll need to use F20.
Secondly, you can consider a partial impression of the thread. This strategy is particularly interesting if you want to easily project the profile using a profile projector. Making a partial impression reduces the extraction constraint and thus allows the use of replicas that are easier to manipulate for inspection (particularly if you want to cut a profile with the Double Blade Cutter, for example). In this second case, F50 will be the most suitable product.
Impression on a Male Thread (External)
For an external thread, it’s preferable to use a product that doesn’t flow. Pasty and malleable products are thus good solutions. Depending on your preferences, you can choose between P35 and M70.
These two products can be cut with the Double Blade Cutter and are thus easy to analyze via a digital vision machine or a profile projector.
Thread with Pitch Less than 0.25mm
The last special case is the thread pitch. If you want to perform an inspection on a very fine pitch, it’s recommended to use a very liquid product. This is even more true if the nominal diameter of the part is small; a liquid product will be much easier to apply.
The F20 is once again the product for the situation!
Conclusion
Replicas are excellent for performing internal and external thread inspections.
Although there are many alternatives to this technique, it remains the fastest, easiest, and most economical to implement. It’s particularly relevant in an Industry 4.0 context as it allows traceability of measurements through the replica in addition to the traceability of measurements.
It’s recommended to use products specially designed for thread inspection. This is the case, for example, with F20, F50, P35, or M70. These are products where taking the impression and extraction is very easy. They are also very easy to use with modern measuring devices, including profile projectors.
When used in combination with a profile projector, these replicas can provide highly accurate and repeatable measurements of both internal and external threads. The profile projector can analyze the replica’s cross-section, providing detailed information about thread pitch, angle, and form that might be difficult or impossible to measure directly on the part.