Quality control is a procedure implemented by companies to ensure product conformity.
It is carried out by a quality controller with (or without) the assistance of other production stakeholders.
Conformity is established based on criteria developed by the company or through mutual agreement between a supplier and a customer. (This includes, for example, industrial metrology.)
This voluntary approach allows companies to address product quality issues in an increasingly demanding market.
Ensuring product quality has become essential for companies, not only to meet customer requirements but also sometimes for legal reasons.
Table of Contents
Introduction to Quality Control
Definition
By definition Quality control represents a procedure (or series of procedures) aimed at ensuring the quality of a manufactured product.
In this perspective, the product must satisfy a defined set of quality criteria and customer requirements.
Caution: Quality Assurance is often associated with Quality Control, but the definitions are not exactly the same!
Unlike the control procedure, which aims to identify potential non-conformities, quality assurance aims to prevent the manufacturing of non-conforming products.
In other words, quality assurance takes place during the product manufacturing process, whereas quality control occurs once the product is finished. The two are often grouped under a single entity.
Generally, this procedure aims to meet current quality standards and thus provide labels or certifications to the company or product.
Conformity and Non-conformity
Before going further, let’s clarify what conformity means!
Conformity is established when the product successfully passes all quality tests.
The product is conforming and can move on to the next step (assembly, marketing, etc.)
When products are non-conforming, it is necessary to take action (or several!) to pass the audit.
A non-conformity is the failure to meet a requirement. This mainly involves detecting the root cause, then addressing the non-conformity: can the product be reworked or should it be scrapped?
Control Missions
The objective of inspection is to detect non-conformities at the right time.
And most importantly, to identify their potential causes and consequences.
Detecting problems is good news for the company.
You are thus able to identify and correct problems when they occur.
There are numerous sources of non-conformity, and it would be concerning to never detect any problems.
Let’s distinguish between two types of controls.
Incoming Inspection
You must ensure that products received from a supplier pass the planned audits.
In this case, since you don’t control the product manufacturing, you must verify that it meets your requirements.
Generally, the audit is performed before putting items into stock.
End-of-Production Control
When you are the product manufacturer, you must also subject your product to examinations.
Indeed, even though you control the production, a malfunction could slip into your process, and you must certify product conformity to your customers.
In this case, quality control allows you to identify malfunctions and address them quickly and reactively.
How to Perform Quality Control
There are different ways of carrying out a control. First of all, let’s distinguish the methods. There are two There are different ways to perform control. First, let’s distinguish between the methods. There are two:
- 100% control, or systematic control. In this methodology, the controller seeks to inspect all pieces in the batch.
- Sampling control. Unlike 100% control, only a portion of the batch is controlled, a representative sample. Both methods have their limitations, but it’s important to understand their main aspects. If you control each piece, you will be limited in several ways:
- The cost will be much higher since you perform more controls.
- You won’t be able to perform destructive testing and will be limited to non-destructive testing techniques. (Including Plastiform! Why not take a look? )
- By controlling at a higher frequency, you increase the risk of human error.
Conversely, sampling control will limit you in terms of performance, as you don’t check everything, so you might miss a defect.
This is quite rare, which is why this methodology is widely used.
The Control Plan
Regardless of your chosen solution, you must have a precise methodology.
The Process Control Plan (PCP) is a formal document that defines the necessary steps to validate the conformity of a process or product.
This document is specific to the product or process.
The plan ensures that the product meets requirements by documenting them. Generally, the PCP is presented in a table format and includes the following elements:
- Identification of control points,
- Characteristics to control (what type? indicator, variable, etc. for example: dimensions in mm.),
- Tolerances,
- Sampling frequency,
- Control method and measuring instrument,
- Actions to take in case of non-conformity.
Don’t forget to properly catalog the plan by assigning it a unique identifier.
Responding to Non-conformity
Detecting a manufacturing defect is a crisis situation.
Indeed, if you notice an anomaly, you’ll have several problems to solve.
First, you’ll need to identify the problem (which isn’t always obvious), then fix it, and run a new series of tests.
During this time, production must stop. Not only will you be unable to produce, but you’ll also need to make corrections to what has already been produced, or worse, lose products entirely.
Therefore, it’s crucial to be reactive and respond quickly during all stages, namely:
- Perform time-efficient controls to detect defects as early as possible (Caution! Quick doesn’t mean rushed!)
- Be reactive in detecting the origin. If you control your product at the very end of the chain, you’ll have many more potential sources of problems than if you perform control at each stage.
- You must also be reactive in bringing the production line back into compliance, which means having a clear and established procedure.
Types of Control
Being reactive also means selecting the right tools.
When it comes to performing product quality control, you have three options:
- Destroy the part by performing destructive testing. This is an expensive and sometimes time-consuming option, but it saves you if you have no alternative.
- Control without destroying through non-destructive testing solutions. Depending on the solution, it takes more or less time, but it’s generally more economical than destroying the part. (Especially if you use Plastiform)
- Delocalized indirect control. This is a specific field of non-destructive testing. The control is no longer performed on the part but on its imprint, and the imprint serves as a measurement witness. (thus facilitating control traceability) Roughness Control – Plastiform process Example of delocalized indirect control
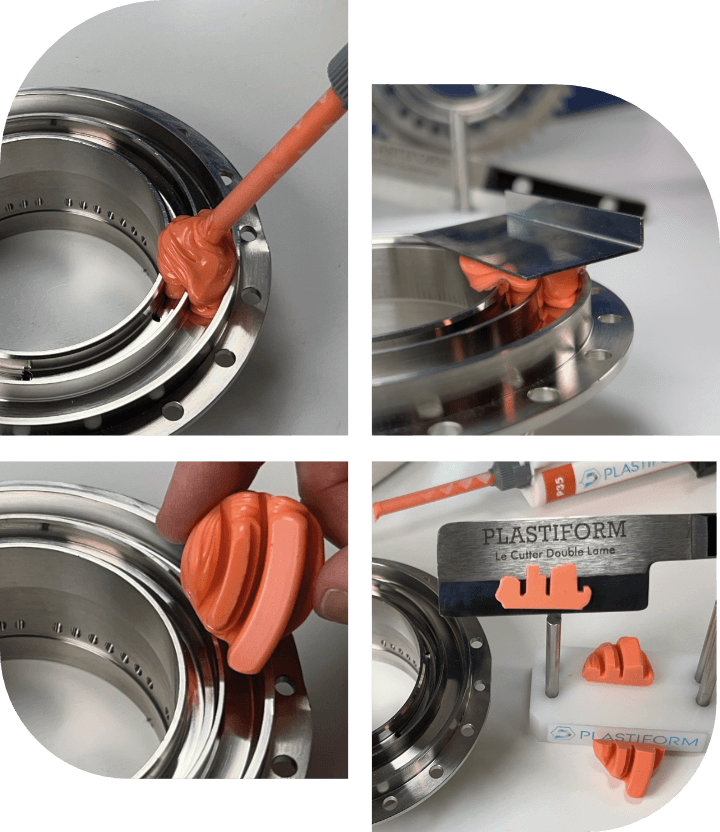
It’s important to determine your control processes in advance with thorough consideration to optimize this process maximally.
It’s also important to implement continuous monitoring to continuously improve your methods.
Conclusion
Today, implementing quality control procedures in companies is essential. Whether for internal concerns about offering quality products or for legal or contractual obligations, quality control is a reality you must face.
There are two types of quality control: incoming inspection and production control. In both cases, the objective is to detect product anomalies.
There are different methodologies for performing quality control. You can first perform 100% control, testing each piece in a batch, or you can opt for sampling control, selecting only a portion of the batch pieces.
In both cases, it’s important to be efficient in detecting and handling non-conformities to avoid penalizing company profitability.
Not quickly detecting a problem’s origin, or worse, the problem itself, could cause production line stoppage or the production of irreparable parts, which is a problem!
Plastiform is an innovative non-destructive testing solution that enables quick and highly effective dimensional or surface condition controls. It’s a solution that takes just a few minutes and leaves an imprint as evidence, which you can request from your supplier to validate incoming inspection.