What is Traceability ? Traceability using Impressions
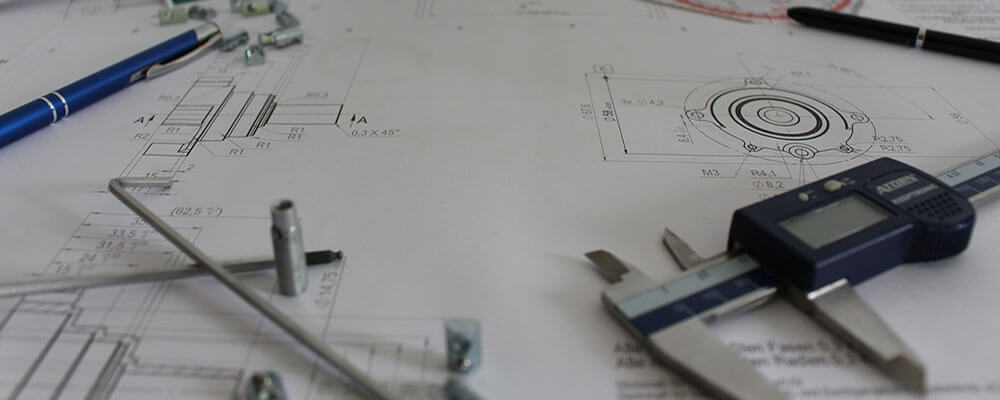
Traceability is a concept that has been in place for over 3800 years, in antiquity. Men used buckets or red irons in order to certify exchanges. Today, traceability is omnipresent in the industry where it makes it possible to provide all the necessary information concerning a product. This information is tracked at each stage of the production chain, from the raw material to the distribution of the product, and even during the wear and tear of the product after its purchase. All sectors make use of this concept in order to produce in a controlled manner. Traceability is defined by the international standard ISO-9001.
Traceability, a simple and understandable definition.
Let’s go back to what we already know in a more understandable way! Traceability means being able to follow your products throughout the production chain. Once you have implemented this concept of systematic tracking, you want to be able to know where, when, by whom and how a product was manufactured. This rigour allows you to improve the quality and safety of your products. To be all the more efficient, traceability is approached from two angles:
- The traceability of the production chain, where you will monitor the product from one manufacturer (or subcontractor) to another.
- Internal traceability, where you will rather seek to monitor the evolution of the product during a process.
Traceability of the production chain
As we have just seen, this is about following the product through its journey, from manufacturer to manufacturer, from raw material to the end of its product life (whether by recycling or destruction). What we are trying to put in place is a history of all the operations carried out on a product, and the associated metrics (dimensions, surface condition, weight, etc.). There are several advantages to implementing this procedure:
- The manufacturer has information to effectively deal with product recalls and identification of production defects,
- The consumer has complete information on the product (origin, composition, etc.),
- The manufacturer may require his subcontractors to justify the conformity of the components he entrusts to them for production.
Of course, the implementation is constraining, you will have to set up detailed procedures and take into account that their realization will be time-consuming.
Internal traceability
In this case, we change perspective! The repository is no longer the production chain but a more specific element that makes it up: the company. Here, we are only interested in the company’s processes, from the suppliers upstream in the chain to the suppliers downstream. In this category, we distinguish more specific sub-categories of internal traceability:
- Process traceability: This involves collecting and processing information during the manufacturing process. This information is attached to the unique identifier attached to the product, so it is very easy to find the information.
- The traceability of the control of the parts: It is a question of setting up a follow-up of the wear of the parts. This includes recurrent wear, but does not include conformity to drawings: were the dimensions correct at the end of machining, for example.
It is important that all monitoring is attached to its reference system (product, process, etc.). This way, you can easily identify flaws and malfunctions and react quickly.
The importance of Traceability
Nowadays the industrial processes are very complex, part of the production can be subcontracted in Asia while the company has another part of the product manufactured by one of its Latin American subsidiaries, all assembled in France. The complexity of the production processes makes it difficult for the company to ensure the quality of its products. Especially since, if a customer notices a malfunction, the manufacturer must be able to identify the origin of the problem in order to ascertain :
- Whether the malfunction is unique or generic,
- Which process/plant is causing the problem.
Traceability is therefore an essential element in product quality control. In particular, in the identification and prevention of risks. If you know the status of a product or component at any time, you can identify the source of a problem much more quickly. In addition, if the malfunction is widespread across an entire production run of the product in question, the company must have the ability to perform a quick recall. (For example, a malfunction on an aircraft engine)
Traceability by Impression
And Plastiform in all this, does it help with traceability?
Of course it does!
Plastiforms allow traceability of several elements:
- The dimensions of a part or a component,
- The roughness of a surface,
- Visual defect inspection.
The impression freezes the condition of the plunger at the time of polymerization. Depending on the product and the application, you can thus keep a material proof of the condition of the part at the time of inspection, which can be very useful for analysis.
So how can I proceed to preserve your Plastiform replicas?
The first important point is that the print must be kept in an airtight bag that is protected from any manipulation. Our prints are shape memory, which means that they retain their shape over time. However, if the impresson is tampered with, there is a risk that it could be damaged. So keep your impressions safe! Then use non-contact measuring instruments! For example, a roughness meter that passes over the same print several times may scratch it with its needle, and this is not the intended purpose!
The case of visual surface inspection
Plastiform also has an important advantage in the special case of visual inspection of defects.
As shown in the picture below, by using Plastiform it is possible to inspect defects on the surface of a part more accurately than on the surface itself.
And as a bonus, you can keep the image of the defect on the impression.
Isn’t that practical?
It is because of its black colour and colorimetric properties that the F30 Visual produces such good results.
Don’t doubt its accuracy, it is capable of copying the printed ink onto a document!

On the left, the original piece, on the right, the reproduction of the surface on Plastiform. Impressive, isn’t it?
Here, for example, is the surface reproduction from our catalogue:
This is quite practical, and in addition, the print can ensure the traceability of a defect.
One might wonder why, if the part is defective, we might as well send it directly, right? Well, it depends on the case, if the defect is found on a part that is difficult to move, or to disassemble, maybe it’s more judicious to simply send the copy in F30 Visual!
It is up to you to evaluate the most interesting approach, but in any case, Plastiform can help you on this point!
Conclusion
Traceability is an essential element in quality control. Tracing products and processes is very important to enable the company to react quickly and efficiently in case of malfunction. The international standards for quality management are grouped in the ISO 9000 series. ISO 9001 is the standard that specifies the concept of traceability in two sections: measurement traceability and identification and traceability. Finally, Plastiform’s fingerprints can help you in traceability operations by preserving the state of the part at the time of the impression.