El Ensayo No Destructivo (END), también llamado Prueba No Destructiva o Evaluación No Destructiva, es una disciplina que reúne procesos y técnicas que permiten medir y garantizar la conformidad e integridad de un material o pieza sin necesidad de destruirlo o alterarlo. El ensayo no destructivo puede incluso evitar el desmontaje o desplazamiento de una pieza.
El uso de técnicas de medición sin destrucción es fundamental para la industria. De hecho, las técnicas de END son muy importantes para una empresa, ya que permiten ahorrar mucho al no destruir piezas que a veces pueden ser muy costosas.
Actualmente, existen varias técnicas muy populares de evaluación no destructiva. La industria de la metrología y el control de calidad perfecciona estas tecnologías año tras año, permitiendo que reemplacen cada vez más el control destructivo, aún muy presente en la industria.
Tabla de contenidos
Principales Aplicaciones del Ensayo No Destructivo
El Ensayos No Destructivos se aplica en casi todos los sectores industriales. En particular: aeronáutica, aeroespacial, industria petrolera, ferroviaria, nuclear, energética, automovilística, etc.
Cuando los operadores utilizan las evaluaciones no destructivas, buscan evidenciar defectos que puedan afectar la conformidad del producto. El operador busca principalmente defectos relacionados con las dimensiones, el desgaste, la geometría o incluso la presencia de imperfecciones.
Las Evaluaciones no destructivas permiten así al fabricante garantizar la conformidad de los productos que vende, pero también al comprador garantizar la conformidad de los productos que recibe. Además, el END permite controlar el desgaste de un producto a lo largo de su vida útil. Esto permite, entre otras cosas, garantizar la seguridad de un producto durante todo su uso, por ejemplo, de un avión en circulación.
Al realizar un examen no destructivo, estamos principalmente en busca de 3 tipos de defectos:
- Una no conformidad con las especificaciones: Medidas dimensionales incorrectas, estado de superficie incorrecto, ángulos incorrectos, etc.
- Defectos de superficie: agujeros, fisuras, picaduras, etc.
- Defectos internos: marcas de desgaste, porosidad, agrietamientos, variaciones de espesor, etc.
Mediante este procedimiento, es posible garantizar la objetividad y la reproducibilidad de un control realizado en una producción. Estos procedimientos se basan en normas (generalmente ISO) con códigos y especificaciones propias de ciertas industrias, y se inscriben en un proceso de gestión de riesgos para la empresa.
Las Técnicas de Ensayo No Destructivo (END)
Existen numerosas técnicas, pero cinco de ellas son particularmente utilizadas por la industria actualmente. Estas cinco técnicas permiten realizar la mayoría de los controles, pero algunas de ellas pueden resultar a veces muy costosas en términos de equipamiento.
La Magnetoscopía
El examen magnetoscópico es un control por campo magnético cuyo valor se define en función de la pieza. Es una de las técnicas de ensayo no destructivo más antiguas (junto con los líquidos penetrantes) que permite, entre otras cosas, detectar discontinuidades superficiales. Sin embargo, esta técnica solo puede aplicarse en materiales ferromagnéticos (materiales sensibles a los imanes).
La magnetoscopía solo permite detectar discontinuidades superficiales o ligeramente subsuperficiales, por ejemplo, grietas, fisuras o fracturas.
Es relativamente simple realizar un ensayo no destructivo magnetoscópico. Basta con magnetizar el área a controlar para crear una fuga del campo magnético hacia las discontinuidades. La fuga atrae las partículas ferromagnéticas hacia la discontinuidad, y es este fenómeno el que permitirá ver el defecto.
Existen varios tipos de equipos para realizar estos controles, generalmente son imanes portátiles o equipos que permiten energizar la pieza.
Finalmente, para facilitar la visualización del defecto, las superficies a menudo se cubren con partículas ferromagnéticas fluorescentes llamadas reveladores.
Los Líquidos Penetrantes
Esta técnica de ensayo no destructivo permite evidenciar únicamente las discontinuidades superficiales. El ensayo por líquidos penetrantes es compatible con una gran variedad de materiales, con excepción de los materiales muy porosos.
Para realizar un examen por líquidos penetrantes, se debe hacer que un producto penetre en las discontinuidades, permitiendo que salga posteriormente.
Para ello, la pieza debe ser recubierta con un líquido llamado “penetrante” coloreado o fluorescente (¡o ambos!). El líquido penetrará entonces por capilaridad dentro de los defectos de la pieza a inspeccionar. Después de un tiempo de reposo, la superficie debe ser limpiada y secada antes de ser nuevamente recubierta con una fina capa de un producto llamado “revelador”, un producto con la capacidad de absorber el líquido penetrante.
Si existe un defecto en la pieza, el revelador evidenciará el penetrante que se ha infiltrado en el defecto, permitiendo que el operador, a simple vista, constate la presencia de discontinuidades superficiales en la superficie.
La Radiografía
Al igual que en la radiografía médica, la radiografía industrial consiste en hacer pasar a través de una pieza un haz de rayos X para irradiar una película colocada detrás de la superficie a inspeccionar. La radiografía puede utilizarse en todos los tipos de materiales.
Los defectos se evidencian por una variación en la densidad óptica de la película. Cuanto mayor es el defecto, más visible será en la radiografía. Por ejemplo, para una superficie de 22 mm de espesor, una porosidad de 2,7 mm será mucho más visible que una porosidad de 1,4 mm.
Varios dispositivos son capaces de realizar una radiografía en la industria, como un acelerador lineal, equipos de gammagrafía o equipos de rayos X, por ejemplo.
El Control por Ultrasonidos
Este método de control busca propagar ondas ultrasónicas dentro de la pieza, que actuarán de forma diferente dependiendo de las discontinuidades y superficies que encuentren. El control por ultrasonidos puede utilizarse en casi todos los materiales, pero el comportamiento de las ondas está influenciado por la estructura de estos (el tamaño del grano, por ejemplo).
La elección de la frecuencia de las ondas permite mejorar la sensibilidad de detección del control. Por ejemplo, una onda de 5 MHz será más sensible. Por otro lado, si la superficie a controlar es rugosa, será preferible utilizar ondas de baja frecuencia, por ejemplo, 2 MHz.
El Control por Moldeo
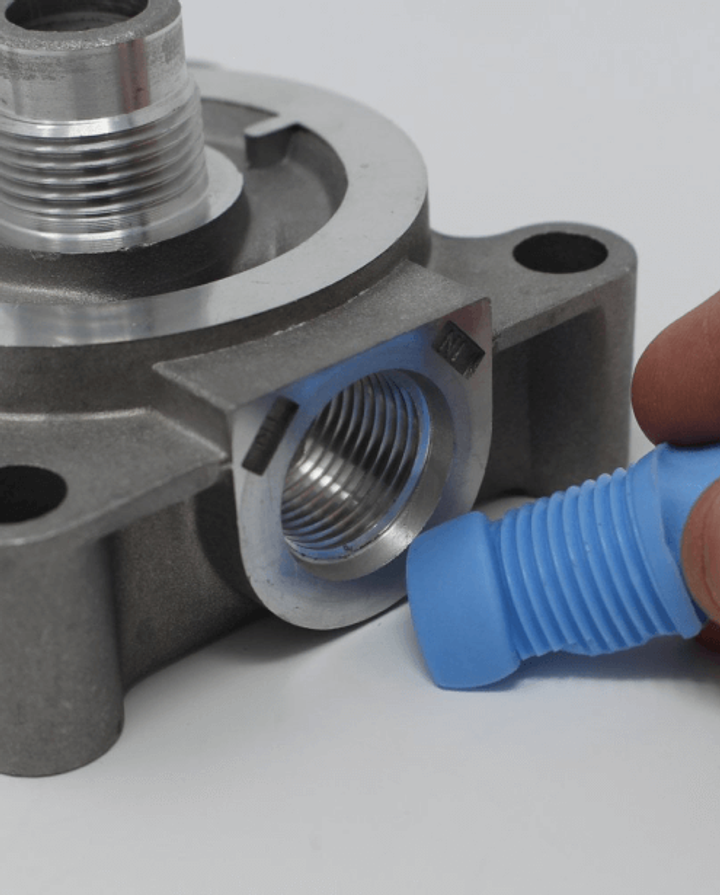
El moldeo es nuestra especialidad en Plastiform. Este procedimiento de control consiste en inyectar un producto originalmente líquido o pastoso en la superficie o en la pieza cuya conformidad se desea verificar. Como los productos son bicomponentes, su contacto en la pieza o en la superficie provoca una reacción de polimerización que endurecerá el líquido.
Una vez que el líquido se endurece, se obtiene una impresión negativa perfecta de la pieza o superficie. Solo hay que extraerla gracias a las propiedades elásticas del producto.
El moldeo, y en particular los Plastiforms, tiene la ventaja de ser utilizable en casi todos los materiales. Sobre todo, permiten evidenciar muchos defectos: dimensiones, ángulos y geometría de la pieza, estado de la superficie, rugosidad superficial, presencia de microdefectos, etc.
Entre las cinco técnicas de ensayo no destructivo presentadas anteriormente, el control por moldeo es una de las menos costosas, con un promedio de 5$ por control.
El Control No Destructivo por Plastiformización
Los controles no destructivos por moldeo son bastante recientes en comparación con otras técnicas y procedimientos utilizados en el sector. Para profundizar un poco más en el tema, detallaré en este artículo algunos de los intereses que puede encontrar al utilizar esta técnica.
Las principales ventajas de la técnica
El primer punto importante es la precisión de los moldes. Aunque la palabra molde pueda tener una connotación bastante negativa en nuestras mentes, los moldes Plastiform tienen una precisión muy alta. Las impresiones son idénticas a la cavidad con una tolerancia de más o menos 1 μm. Esta precisión es aún más importante cuando se utilizan equipos de calidad para analizarlas. Por ejemplo, con máquinas de medición sin contacto (proyectores de perfil, interferómetros, etc.), se obtendrá mejor precisión que con una máquina de medición con contacto.
El segundo punto, también muy interesante, es la trazabilidad que pueden proporcionar los moldes. Los moldes Plastiforms, una vez extraídos, no cambian, es decir, sus dimensiones o los defectos que han capturado permanecerán, incluso años después. Gracias a esta especificidad, es posible para las empresas garantizar la trazabilidad de sus controles, conservando los moldes y las mediciones realizadas con ellos.
PRUEBE PLASTIFORM AHORA MISMO
El maletín contiene todos los accesorios necesarios para usar Plastiform. ¡Es la mejor manera de probar nuestras soluciones por primera vez!
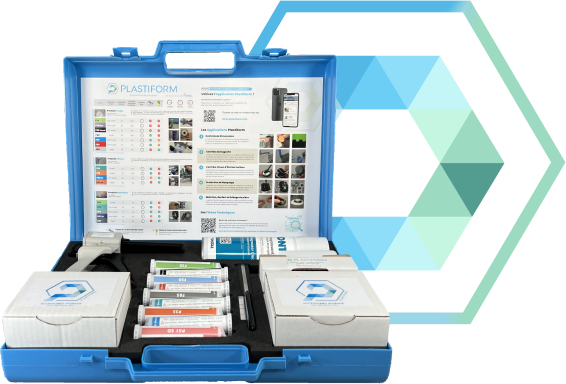
También, como se mencionó un poco antes, el moldeo es un proceso bastante económico, cuyo costo se estima en alrededor de 5$ por control. Este bajo costo permite a las empresas realizar controles sistemáticos en su producción sin sacrificar tiempo ni dinero.
Por último, una enorme ventaja que pueden tener los productos de moldeo, y en particular los que comercializamos en Plastiform, es que es posible aplicarlos sin mover o desmontar la pieza. Si se detectan defectos en una producción que requiere el control de productos en circulación (por ejemplo, aviones), no será necesario desmontarlos para realizar el control con el molde. Esta particularidad, aunque quizás un poco situacional, a veces ahorra mucho dinero y tiempo a las empresas que podrían encontrarse en dificultades en un caso como este.
En otras palabras, los controles no destructivos por moldeo (o por Plastiformización) son un método muy práctico para verificar la conformidad de una pieza, pero también para medir su desgaste a lo largo del tiempo.
Conclusión
Para concluir este artículo, cada método de control no destructivo ofrece diferentes parámetros a considerar. Es importante tener en cuenta el tipo de discontinuidad que se busca, el material en el que se busca esta discontinuidad y cuáles son las restricciones de la empresa.
No existe una técnica mejor que todas las demás. Cada técnica tiene sus propios puntos fuertes que a veces la hacen obvia para realizar un control no destructivo. Corresponde al inspector decidir qué técnica necesita y cómo implementarla. Por lo tanto, es importante hacer un balance para determinar si no hay una mejor manera de proceder para ganar en precisión, tiempo y dinero.